Manufacturing
Hopper for Powder Bed Fusion Additive Manufacturing
Principal Investigator : MAE, Prof Chua Chee Kai
Key Features and Innovation
- Multi-material hopper enables powder bed fusion technology to fabricate multi materials in 2 axes.
- It is able to combine materials with different materials which are conventionally difficult to be welded together, e.g. copper and stainless steel.
Potential Application
- Applicable to industries that require multi-material components e.g. heat transfer components, corrosion prevention parts, implants, electricity, gas and air-conditioning supply and transportation and storage sectors
Figure 1. Prototype of Hopper for powder
bed fusion
Figure 2. Samples of multi materials parts produced by SLM
Method of Forming Titanium-tantalum Alloys
Principal Investigator : MAE, Asst Prof Yeong Wai Yee
Key Features and Innovation
- Homogeneous titanium-tantalum alloy is obtained using selective laser melting (SLM) for the first time.
- The resulting titanium-tantalum alloy has comparable mechanical strength to Ti6Al4V, and is more suitable for biomedical applications due to its lower Young’s modulus.
- In vitro testing has also confirmed titanium-tantalum’s biocompatibility to be comparable to Ti6Al4V and pure titanium.
- Functional parts, with complex geometries, can be produced using the alloys in a single step, simultaneously with the alloying process.
Relevance to which Industry
- Manufacturing
- Health and Social Services
- Professional, Scientific and Technical Activities
- Biomedical (devices)
- Materials

Figure 1. Implants fabricated using
SLM
Figure
2. Complex
lattice structures fabricated using SLM
Self-cleaning and Anti-icing Coatings
Principal Investigator : MSE, Prof Chen Zhong
Key Features and Innovation
- Mechanically durable, UV-resistant, and can be made transparent when necessary.
Potential Application
- Solar panel, wind turbine, power transmission facilities, sports equipment, windshield of automobiles, and building windows, etc
Relevance to which Industry
- Manufacturing
- Energy
- Precision Engineering and etc.
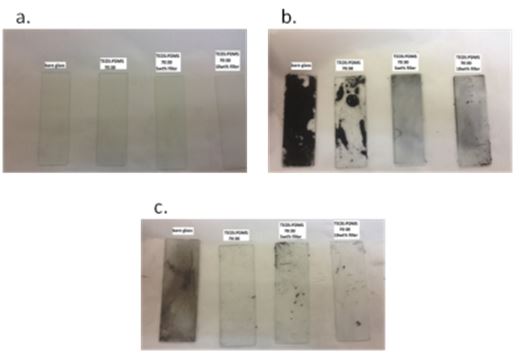
Figure 1. Photographic images showing (a) pristine coatings, (b)
coatings after dirt spray, and (c) coatings after water spray for cleaning. In
each image from left to right: bare glass (no coating), coating No.1, coating
No. 2, and coating No. 3.
